Plastic extrusion for efficient, flexible manufacturing solutions
Plastic extrusion for efficient, flexible manufacturing solutions
Blog Article
Key Advantages and Factors To Consider of Implementing Plastic Extrusion in Your Projects

Comprehending the Fundamentals of Plastic Extrusion
Plastic extrusion, a staple in the production industry, is a process that involves melting raw plastic material and reshaping it into a continual profile. This account, once cooled down, can be cut into desired sizes or coiled for later use. The appeal of plastic extrusion hinges on its flexibility. A large range of items, from piping to home window frames, can be created. The process calls for an extruder, an intricate machine with a warmed barrel, a revolving screw, and a die at the end. The plastic material, in the type of pellets, is fed right into the extruder, where it's thawed and compelled through the die, taking its shape. The choice of plastic and the style of the die identify the item's attributes.
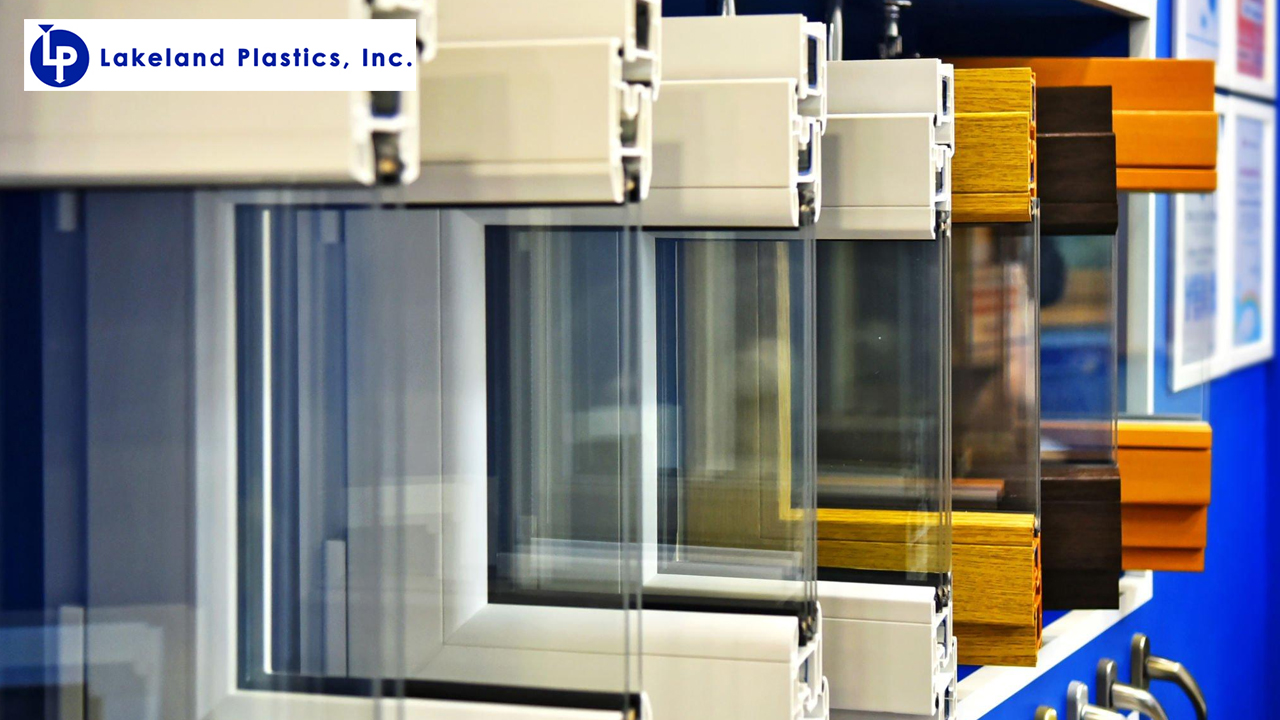
The Economic Benefit of Plastic Extrusion
The economic advantage of plastic extrusion lies primarily in 2 locations: economical material production and valuable production speeds. With plastic extrusion, businesses can generate high volumes of product at a reduced expense contrasted to other methods. Moreover, the process flaunts an excellent production rate, substantially reducing time and more boosting its financial feasibility.
Cost-Effective Product Production
A considerable advantage of plastic extrusion is its exceptional cost-effectiveness. This manufacturing process enables continual, high-volume production with very little waste, which converts right into reduced costs. The raw materials used, typically plastic pellets, are relatively cost-effective contrasted to other compounds (plastic extrusion). The procedure itself calls for less power than numerous various other manufacturing techniques, even more decreasing prices. In addition, the extrusion process allows for a high degree of accuracy fit the plastic, lowering the need for costly post-production modifications or improvements. The resilience and durability of extruded plastic items frequently mean much less require for substitutes, contributing to long-term financial savings. All these aspects make plastic extrusion an extremely affordable selection for many jobs, supplying an appealing equilibrium in between expense and performance.
Beneficial Production Speeds
While maintaining the cost-effectiveness of the products, an additional notable advantage of plastic extrusion depends on its rapid manufacturing rates. This performance in the manufacturing process is credited to the continuous nature of the extrusion procedure, permitting high-volume production in a fairly short time period. The rate of production directly correlates to a decrease in labor costs and a rise in outcome, thereby boosting the total economic practicality of the process. The hectic manufacturing does not endanger the high quality of the last product, guaranteeing regular and trusted outcomes. This mix of cost-effectiveness, rate, and high quality highlights the substantial economic benefit of carrying out plastic extrusion in numerous projects.
Convenience and Personalization: The Strengths of Plastic Extrusion
One of the famous staminas of plastic extrusion exists in its adaptability and personalization possibility. These qualities unlock to endless design possibilities, offering suppliers the ability to customize products to specific needs. This enhanced degree of customization not only boosts item performance however additionally considerably enhances item uniqueness.
Unrestricted Design Opportunities
Plastic extrusion beams in its capacity to provide virtually limitless design opportunities. This technique supplies freedom to produce elaborate accounts Web Site and complicated shapes, an accomplishment difficult to accomplish with various other manufacture techniques. Owing to the fluid nature of molten plastic, the process is versatile sufficient to generate a diverse variety of measurements, kinds, and dimensions. The plastic can be adjusted to match distinct requirements, enabling the manufacturing of personalized geometries and conference details customer needs. Plastic extrusion can deal with a range of plastic types, broadening its application extent. This adaptable method, for that reason, serves a large range of industries from building and construction to automobile, product packaging to electronics, and beyond. With plastic extrusion, the style possibilities are practically unlimited.
Increasing Item Individuality
The convenience of plastic extrusion can greatly enhance product originality. This procedure allows designers to experiment with various forms, sizes, and shades, offering them the flexibility to produce one-of-a-kind products that attract attention in the marketplace. It is this customization that provides a distinct identification to each item, identifying it from its rivals.
In enhancement to its visual benefits, the customizability of plastic extrusion additionally supplies functional advantages. Therefore, plastic extrusion not only enhances product individuality however also its energy and bankability.
Layout Limitations in Plastic Extrusion: What You Need to Know
How can create restrictions potentially affect the process of plastic extrusion? While plastic extrusion is flexible, design restrictions can cut its benefits. Specific complicated designs may not be viable because of the restrictions of the extrusion process, potentially limiting the development of intricate profiles. The procedure is less ideal for multi-chambered or hollow frameworks. Furthermore, the extrusion process may not constantly offer the preferred surface coating, particularly for those requiring high gloss or optical clarity. Material choice can additionally present difficulties, as not all polymers appropriate for extrusion. High-temperature immune plastics, as an example, might provide problems. Recognizing these constraints is vital for efficient execution of plastic extrusion in your projects. plastic extrusion.
Reviewing the Ecological Impact of Plastic Extrusion
While recognizing design limitations is a significant facet of plastic extrusion, it is equally important to consider its environmental implications. The process of plastic extrusion entails melting plastic materials, potentially launching damaging gases right into the setting. Utilizing recycled plastic materials in the extrusion process can reduce ecological influence.
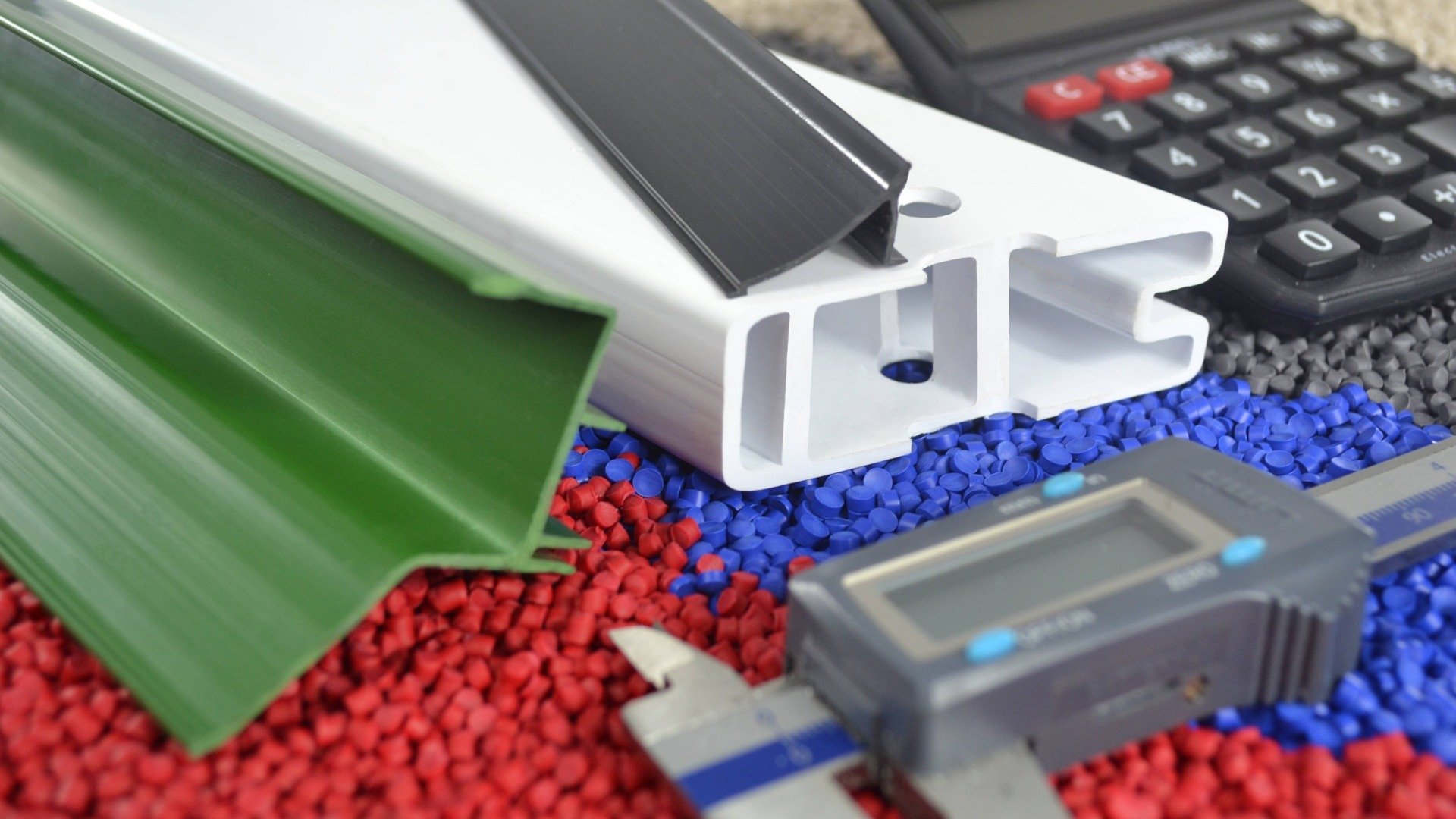
Study: Successful Projects Using Plastic Extrusion
Success tales in the field of plastic extrusion abound, showing both the adaptability and effectiveness of this manufacturing procedure. One significant instance is the development of PVC pipes made use of in modern-day plumbing. This process involves melting plastic and developing it right into a continuous tube, providing considerable cost and resilience advantages. An additional successful instance is the manufacturing of plastic movie for product packaging and agriculture. With extrusion, producers can create extremely personalized, slim, and durable films. Automotive sectors additionally benefit, utilizing extruded plastic for parts like trim or seals, improving car durability. These instances highlight plastic extrusion's important function in numerous industries, confirming to its flexibility, cost-effectiveness, and trusted output.
Final thought
In final thought, plastic extrusion uses a efficient and cost-effective approach for creating complex shapes with marginal waste. Including plastic extrusion right into jobs can lead right here to successful site results, as confirmed by countless instance researches.
Plastic extrusion, a staple in the manufacturing industry, is a procedure that involves melting raw plastic material and improving it into a continuous account. Plastic extrusion can deal with a range of plastic kinds, increasing its application extent.How can create restrictions potentially affect the procedure of plastic extrusion? The process of plastic extrusion involves melting plastic materials, possibly releasing harmful gases into the setting. Making use of recycled plastic materials in the extrusion process can reduce environmental impact.
Report this page